How To Calculate The Cost Per Unit
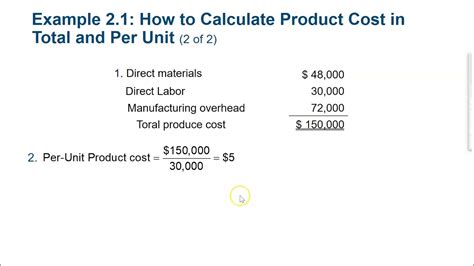
Calculating the cost per unit is a fundamental aspect of business and financial analysis, providing valuable insights into the profitability and efficiency of a product or service. This comprehensive guide will walk you through the steps to accurately determine the cost per unit, helping you make informed decisions and optimize your operations. Whether you're a seasoned entrepreneur or just starting out, understanding this crucial metric is essential for success.
Understanding Cost Per Unit

The cost per unit represents the total expenses incurred to produce or provide a single unit of a product or service. It serves as a vital tool for pricing strategies, cost control, and financial planning. By breaking down the costs associated with each unit, businesses can assess their profitability, identify areas for cost reduction, and make data-driven decisions.
Calculating the cost per unit involves considering various expenses, including raw materials, labor, overhead costs, and any other associated expenses. It provides a clear picture of the true cost of production or service delivery, allowing businesses to set competitive prices and maintain a healthy profit margin.
Step-by-Step Guide to Calculating Cost Per Unit

Here’s a detailed breakdown of the process to help you calculate the cost per unit accurately:
Step 1: Identify Direct Costs
Direct costs are those directly attributable to the production or provision of a specific unit. These costs typically include raw materials, direct labor, and any other expenses that vary with production volume. To identify these costs, consider the following:
- Raw Materials: Calculate the cost of all materials used in the production process, including the quantity and cost per unit of each material.
- Direct Labor: Determine the wages and benefits associated with the labor directly involved in producing the unit. This may include production workers, supervisors, and any specialized labor.
- Other Direct Costs: Identify any additional costs directly tied to the production process, such as utilities, equipment rental, or specialized services.
Step 2: Calculate Overhead Costs
Overhead costs, also known as indirect costs, are those that support the production process but cannot be directly attributed to a specific unit. These costs are essential to consider as they contribute to the overall operational expenses. Here’s how to calculate them:
- Rent and Utilities: Include the cost of rent, electricity, water, and other utilities necessary for the production facility.
- Depreciation: Calculate the depreciation of machinery, equipment, and other assets used in production. This can be done using various methods such as straight-line depreciation or accelerated depreciation.
- Insurance and Maintenance: Consider the cost of insurance for the production facility and equipment, as well as any maintenance and repair expenses.
- Administrative and Office Expenses: Factor in costs related to administrative staff, office supplies, and other general overhead expenses.
- Marketing and Advertising: Include expenses incurred for marketing and advertising campaigns to promote the product or service.
Step 3: Allocate Overhead Costs
Once you have calculated the overhead costs, the next step is to allocate them to the specific units produced. There are several methods to allocate overhead costs, and the choice depends on the nature of your business and the accuracy required. Here are a few common methods:
- Activity-Based Costing (ABC): This method allocates overhead costs based on the activities performed during the production process. It considers the specific resources and activities involved in producing each unit.
- Traditional Costing: Traditional costing allocates overhead costs based on a single cost driver, such as labor hours or machine hours. While simpler, it may not accurately reflect the true cost of production.
- Machine-Hour Rate: If machine hours are a significant cost driver, this method allocates overhead costs based on the number of machine hours used in production.
Step 4: Calculate Total Costs
Now that you have identified and allocated the direct and overhead costs, it’s time to calculate the total costs. Sum up all the direct costs and overhead costs allocated to each unit. This total cost represents the expense incurred to produce or provide a single unit.
Step 5: Determine Cost Per Unit
Finally, to calculate the cost per unit, divide the total cost by the number of units produced. This will give you the average cost per unit. It’s important to note that this calculation provides an average cost, and actual costs may vary slightly due to factors like material waste, labor efficiency, or other variables.
Cost Category | Cost per Unit |
---|---|
Raw Materials | $[Raw Material Cost per Unit] |
Direct Labor | $[Direct Labor Cost per Unit] |
Overhead Costs | $[Allocated Overhead Cost per Unit] |
Total Cost per Unit | $[Total Cost per Unit] |

Benefits of Accurate Cost Per Unit Calculation
Understanding and accurately calculating the cost per unit offers numerous advantages for businesses. Here are some key benefits:
- Pricing Strategy: With precise cost information, businesses can set competitive prices that ensure profitability while remaining attractive to customers.
- Cost Control: By identifying cost drivers and areas for improvement, businesses can implement cost-saving measures and optimize their operations.
- Financial Planning: Accurate cost per unit calculations provide valuable insights for financial forecasting, budgeting, and decision-making.
- Profitability Analysis: This metric allows businesses to assess the profitability of individual products or services, helping them focus on the most profitable offerings.
- Decision-Making: Cost per unit calculations support strategic decisions, such as product mix, expansion plans, or investment choices.
Case Study: Implementing Cost Per Unit Analysis
Let’s consider a hypothetical case study to illustrate the practical application of cost per unit analysis. Imagine a small bakery, Sweet Treats Bakery, specializing in producing and selling custom cakes.
To calculate the cost per unit for their signature cake, Sweet Treats follows these steps:
- Identifying Direct Costs:
- Raw Materials: Flour ($0.25/cup), Sugar ($0.15/cup), Eggs ($0.50/dozen), Butter ($0.80/stick), and Custom Flavored Frosting ($1.20/cup)
- Direct Labor: Baking and Decorating Staff ($15/hour)
- Calculating Overhead Costs:
- Rent ($1,500/month)
- Utilities ($300/month)
- Depreciation of Bakery Equipment ($500/month)
- Insurance ($200/month)
- Marketing ($250/month)
- Allocating Overhead Costs: Using Activity-Based Costing, they allocate overhead costs based on the number of cakes produced.
- Calculating Total Costs: Sum up all direct and allocated overhead costs for each cake.
- Determining Cost Per Unit: Divide the total cost by the number of cakes produced to find the cost per unit.
Through this analysis, Sweet Treats Bakery gains a clear understanding of the true cost of producing their signature cake, allowing them to set an appropriate selling price and make informed decisions to improve profitability.
Conclusion: Empowering Your Business with Cost Per Unit Calculation

Calculating the cost per unit is a powerful tool for businesses to gain financial insight and make strategic decisions. By following the step-by-step guide outlined above, you can accurately determine the cost per unit of your products or services. This knowledge empowers you to optimize pricing, control costs, and enhance profitability. Remember, regular reviews and adjustments are crucial to staying ahead in a dynamic business environment.
Stay tuned for more expert guides and industry insights to help you navigate the world of business and finance with confidence.
How often should I review and update my cost per unit calculations?
+It’s recommended to review your cost per unit calculations regularly, ideally on a quarterly basis. This allows you to account for any changes in costs, production volumes, or market conditions. By staying updated, you can make timely adjustments to your pricing strategy and operational decisions.
What happens if my cost per unit exceeds my selling price?
+If your cost per unit exceeds your selling price, it indicates that your business is operating at a loss for that particular product or service. In such cases, it’s crucial to review your costs and consider strategies to reduce expenses or adjust your pricing. This may involve negotiating with suppliers for better deals, optimizing production processes, or exploring alternative sourcing options.
Can cost per unit calculations vary for different products within the same business?
+Yes, cost per unit calculations can vary significantly between different products or services within the same business. Each product may have unique direct and overhead costs, production processes, and cost drivers. It’s essential to calculate the cost per unit for each product individually to ensure accurate pricing and profitability analysis.