Shipment Exception Meaning
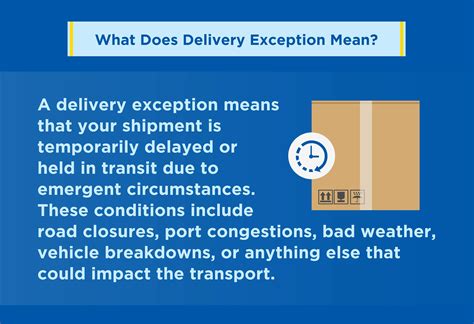
In the world of logistics and supply chain management, understanding shipment exceptions is crucial for efficient operations and customer satisfaction. Shipment exceptions refer to unexpected events or circumstances that occur during the transportation of goods, leading to deviations from the originally planned delivery process. These exceptions can arise due to various factors, such as weather conditions, equipment failures, customs delays, or even human errors. Effectively managing and resolving shipment exceptions is essential to ensure timely deliveries, minimize costs, and maintain positive relationships with customers.
Common Types of Shipment Exceptions

Shipment exceptions can manifest in several forms, each requiring unique handling strategies. Here are some of the most common types of shipment exceptions:
Delay in Transit
Delays in transit are perhaps the most frequent shipment exception. These delays can be caused by a range of factors, including adverse weather conditions, traffic congestion, or mechanical issues with the transportation vehicle. For instance, a snowstorm in a key shipment route might lead to a significant delay in the delivery of goods, impacting the estimated time of arrival (ETA) and potentially causing disruptions in the supply chain.
Damaged Goods
Damage to goods during transit is another critical exception. This can occur due to rough handling, inadequate packaging, or accidents during loading and unloading processes. For example, fragile electronics may be susceptible to damage if not packaged properly, resulting in costly repairs or replacements.
Customs and Regulatory Issues
International shipments often face challenges related to customs and regulatory compliance. Delays can occur due to incomplete or inaccurate documentation, inspections, or changes in import/export regulations. Navigating these complexities requires expertise and timely action to avoid costly penalties and delays.
Shortages and Overages
Inaccurate counting or loading can lead to shortages or overages in shipments. This can create significant challenges, especially when dealing with perishable goods or products with strict quantity requirements. For instance, a shortage in a shipment of medical supplies could have serious implications for healthcare facilities.
Address Errors
Incorrect or incomplete address information can result in shipment exceptions. This might lead to missed deliveries, returned shipments, or additional costs for address correction and redelivery.
Impact of Shipment Exceptions

Shipment exceptions can have far-reaching consequences for businesses and their customers. These impacts can be both financial and operational, affecting the bottom line and customer relationships.
From a financial perspective, shipment exceptions can lead to increased costs for businesses. Delays in transit may result in additional transportation fees, storage costs, or penalties for missed delivery windows. Damaged goods might require costly repairs or replacements, impacting profit margins. Moreover, customs delays can lead to late fees, increased inspection costs, or even seizure of goods, resulting in significant financial losses.
Operationally, shipment exceptions can disrupt supply chains, leading to stockouts, production delays, or missed sales opportunities. For example, a delay in the delivery of raw materials to a manufacturing plant can halt production, causing a ripple effect throughout the supply chain. Similarly, shortages or overages in shipments can lead to inventory management issues, affecting the accuracy of stock levels and purchase planning.
Strategies for Managing Shipment Exceptions
Effectively managing shipment exceptions requires a proactive approach and the implementation of robust strategies. Here are some key strategies that can help mitigate the impact of shipment exceptions:
Advanced Tracking and Visibility
Investing in advanced tracking technologies and real-time visibility solutions can provide valuable insights into the location and condition of shipments. This enables logistics teams to identify potential exceptions early on and take proactive measures to mitigate their impact. For instance, GPS tracking can help identify traffic delays, while temperature sensors can alert to potential issues with refrigerated shipments.
Robust Packaging and Handling Procedures
Implementing rigorous packaging standards and training staff on proper handling procedures can significantly reduce the risk of damage during transit. This includes using appropriate packaging materials, securing goods adequately, and ensuring proper loading and unloading practices.
Customs Expertise and Documentation
Navigating the complexities of international trade requires expertise in customs regulations and documentation. Businesses should invest in training their logistics teams or partnering with customs brokers to ensure compliance and minimize delays. Maintaining up-to-date knowledge of changing regulations and utilizing digital tools for accurate documentation can streamline the customs process.
Regular Communication with Carriers
Maintaining open lines of communication with carriers is crucial for identifying potential exceptions early on. Regular updates on transit status, weather conditions, or equipment issues can help logistics teams anticipate and plan for potential delays. Building strong relationships with carriers can also lead to faster resolution of exceptions and improved overall service.
Exception Management Software
Implementing exception management software can automate many of the processes involved in handling shipment exceptions. This software can provide real-time alerts, track exceptions, and offer recommendations for resolution. By centralizing exception data, businesses can gain valuable insights into the root causes of exceptions and take proactive measures to prevent their recurrence.
The Future of Shipment Exception Management
As technology continues to advance, the future of shipment exception management looks promising. Artificial intelligence (AI) and machine learning algorithms are already being utilized to predict potential exceptions and optimize routing and scheduling to minimize their impact. Additionally, blockchain technology can enhance supply chain transparency and security, reducing the likelihood of exceptions due to fraud or errors.
Furthermore, the increasing adoption of electric and autonomous vehicles in logistics can lead to more efficient and predictable deliveries, reducing the frequency of exceptions caused by mechanical failures or driver errors. However, it is essential to recognize that technology alone cannot solve all issues. Human expertise and judgment will always be critical in effectively managing shipment exceptions, especially in complex or unexpected scenarios.
Conclusion

In the dynamic world of logistics, shipment exceptions are an inevitable part of the process. However, by understanding the various types of exceptions, their impacts, and effective management strategies, businesses can minimize the disruption caused by these exceptions. Investing in technology, expertise, and robust processes can help create a resilient supply chain that is better equipped to handle unexpected challenges. Ultimately, effective shipment exception management is crucial for maintaining a competitive edge, ensuring customer satisfaction, and driving business success in the highly competitive logistics industry.
What are the key challenges faced in managing shipment exceptions?
+Managing shipment exceptions can be challenging due to the dynamic nature of logistics operations. Some key challenges include the unpredictability of weather conditions, the complexity of international regulations, and the potential for human errors. Additionally, the need for real-time visibility and rapid response to exceptions can be resource-intensive, requiring advanced technologies and well-trained staff.
How can businesses reduce the financial impact of shipment exceptions?
+To mitigate the financial impact of shipment exceptions, businesses can implement strategies such as insurance coverage for high-value or vulnerable goods, negotiating flexible delivery terms with carriers, and building buffer time into delivery schedules to account for potential delays. Additionally, investing in technology that provides real-time visibility can help businesses identify and address exceptions early, reducing the likelihood of costly disruptions.
What role does customer communication play in shipment exception management?
+Effective customer communication is crucial in shipment exception management. By keeping customers informed about potential delays or issues, businesses can manage customer expectations and maintain trust. Timely and transparent communication can also help businesses gather valuable feedback, identify areas for improvement, and potentially resolve exceptions before they escalate.